A few years ago, Boyd Johnson (of Boyd Wheels) and I were sharing a beer and he mentioned someday wanting to make braided carbon fiber rims. Fast forward to today, and it’s now a reality.
He and a few others have acquired Munich Composites in Germany, which has been making braided carbon fiber rims for several German brands. As part of the acquisition, they’re moving half of their production line to Landrum, SC, to produce for the North American market.
Now, they offer US-based alloy rim construction via Olive Manufacturing Group, and carbon via Munich Composites. This lets EU customers keep ordering from Europe, saving on VAT and other fees, and opens up more opportunities for US and Canadian brands to onshore future products.
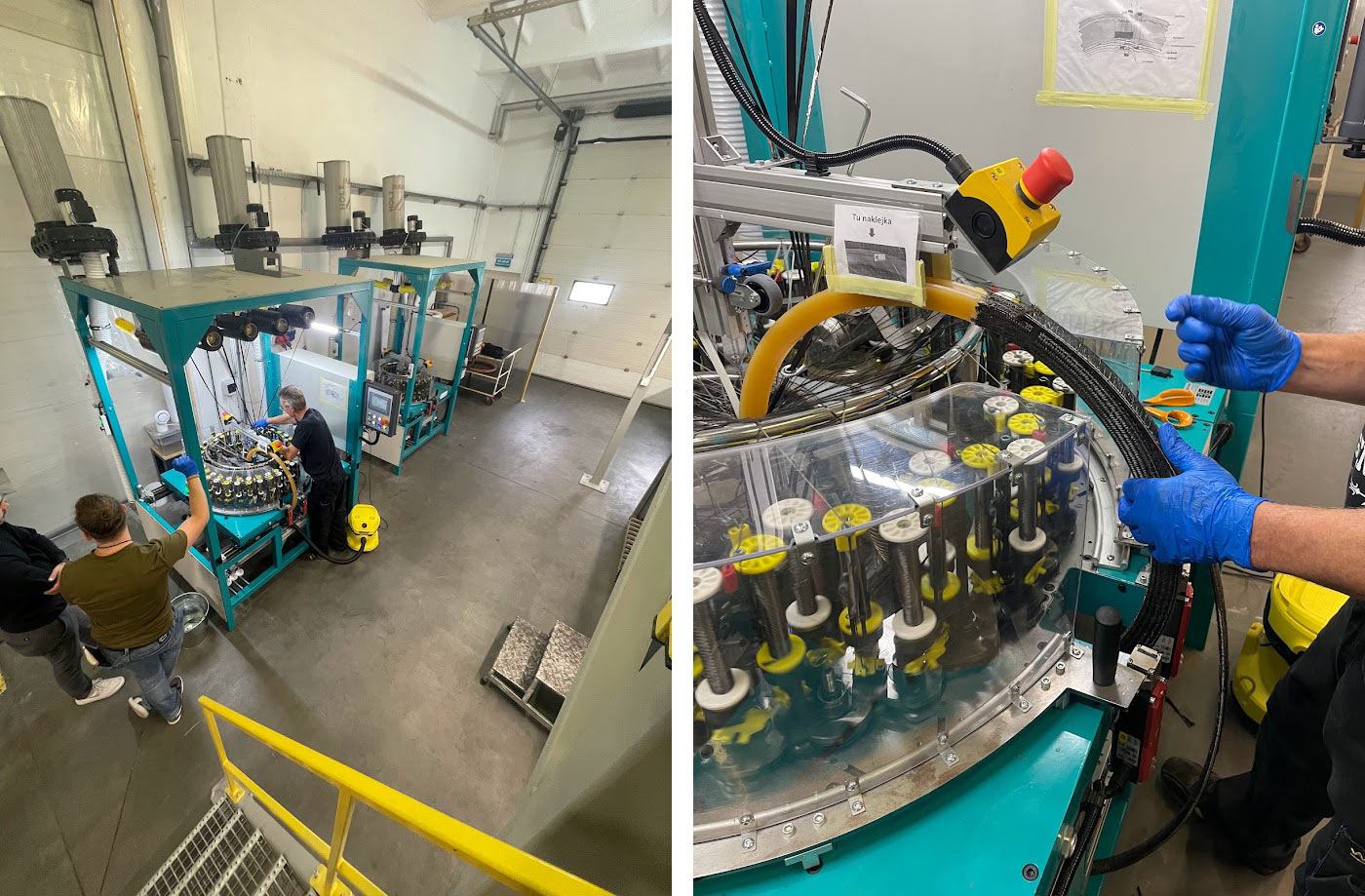
The process weaves continuous carbon fiber strands into a “sock” that slides over or is directly woven around a mold. The part is then inserted into the outer mold and injected with resin. Called RTM (Resin Transfer Molding), the part starts with dry fibers and the resin is added under high pressure. Time Bicycles has used this method for years.
Munich Composites GmbH says their patented braiding construction creates a stronger, higher quality rim because it has continuous fiber throughout the entire rim rather than hundreds of small pre-preg carbon pieces that are placed by hand. It’s not just the continuous fibers, they can also control the exact resin volume and mix, and easily add other fiber types (kevlar, Aramid, etc.) to the construction.
They’re partnering with Clemson University, which will allow them to even higher-pressure molding in the future, which could create a more advanced product than what’s currently done in the bike industry.
Boyd will use the new technology in future products, but Hunt Bike Wheels will beat them to it with a new wheelset using woven rims at Sea Otter.