Now it’s no secret that I love cool gadgets, so when Kevin came across our Must Have RV Upgrades Article and invited us to come out to the MicroAir headquarters and get a behind the scenes look at how they operate we were there the next day. Not many things are made here anymore, but pulling up out front you can see that they are proud of the fact that all of their products are.
Not just assembled here from components manufactured somewhere else, Made here, Assembled by hand, and every single product quality tested at multiple points throughout their manufacturing process.
The first thing I notice when we walk in the door is chatter, like the kind that stops when the boss walks in the room most places. I didn’t realize this was the first thing I noticed until much later in our visit. Kevin met us in the lobby and showed us to the conference table so we could sit and chat for a bit before taking a walk through the production line.
As we chat with Kevin about Micro-Airs product line and history people walk by, all with a friendly wave and a hello, on their way to where ever it was they were going. We continued talking with Kevin about the expanding line of products they make, and how they are designed and built right here.
The first stop on our tour was the design room. The first thing that came to mind was The Matrix. There were work stations with multiple monitors with designs of circuit boards to come next to prototypes next to pieces that had passed and failed quality control checks so they could be dissected and retooled to make improvements for future generations of products.
Further down the hallway is the door to the factory floor. On the other side of that door is an assembly line so efficient that it would make Henry Ford take notice. Micro-Air has been getting more and more orders, and has been starting to outgrow the amount of space they have, so in turn has set up their factory floor to use every inch of available space to increase production without sacrificing quality.
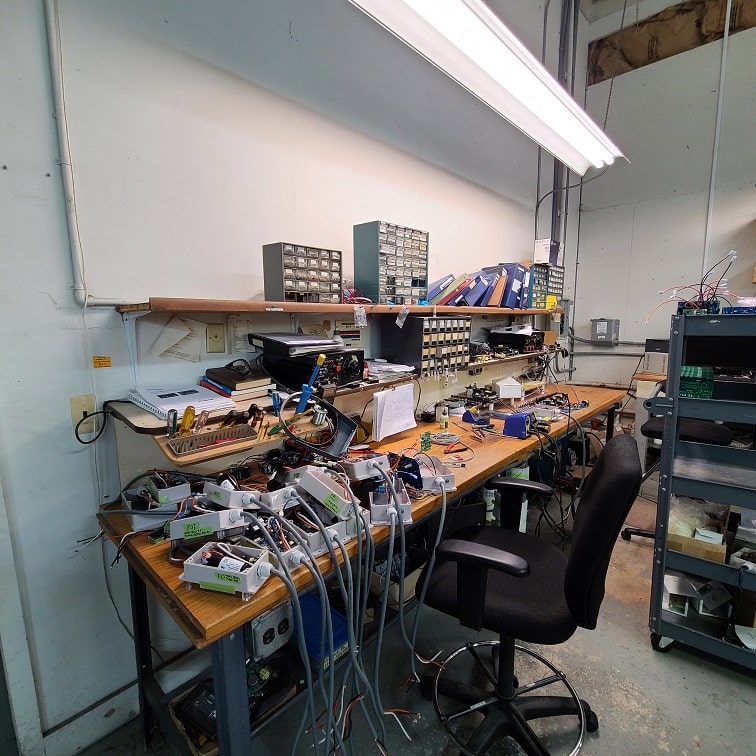
The very first station we see is the retooling station. The retooling station is basically the “oops pile”. Kevin made it a point to bring out attention to it, which at first I thought was odd, because we could have just walked right past it to the very next station where assembly was being done.
I thought to myself ‘why would you point out your oops pile when you should be showing us how awesome your factory is?’
Well, it turns out Kevin is smarter than I am, and by showing us the oops pile he was showing us how awesome they are. At the conclusion of every station along the assembly line is a quality control check. Now when I say every station, I mean every station. QC is done after each set of components goes into each product, not just at the end of the line.
If at any point during the entire process a piece fails its quality check, it is labeled with where it was in the process and brought here. If its a piece that needs a reworking on the schematic it can go right through the door to the left and into the design room for its update. If its a piece that just needs an extra bit of solder, it can get that and be returned back into the work flow at the appropriate station.
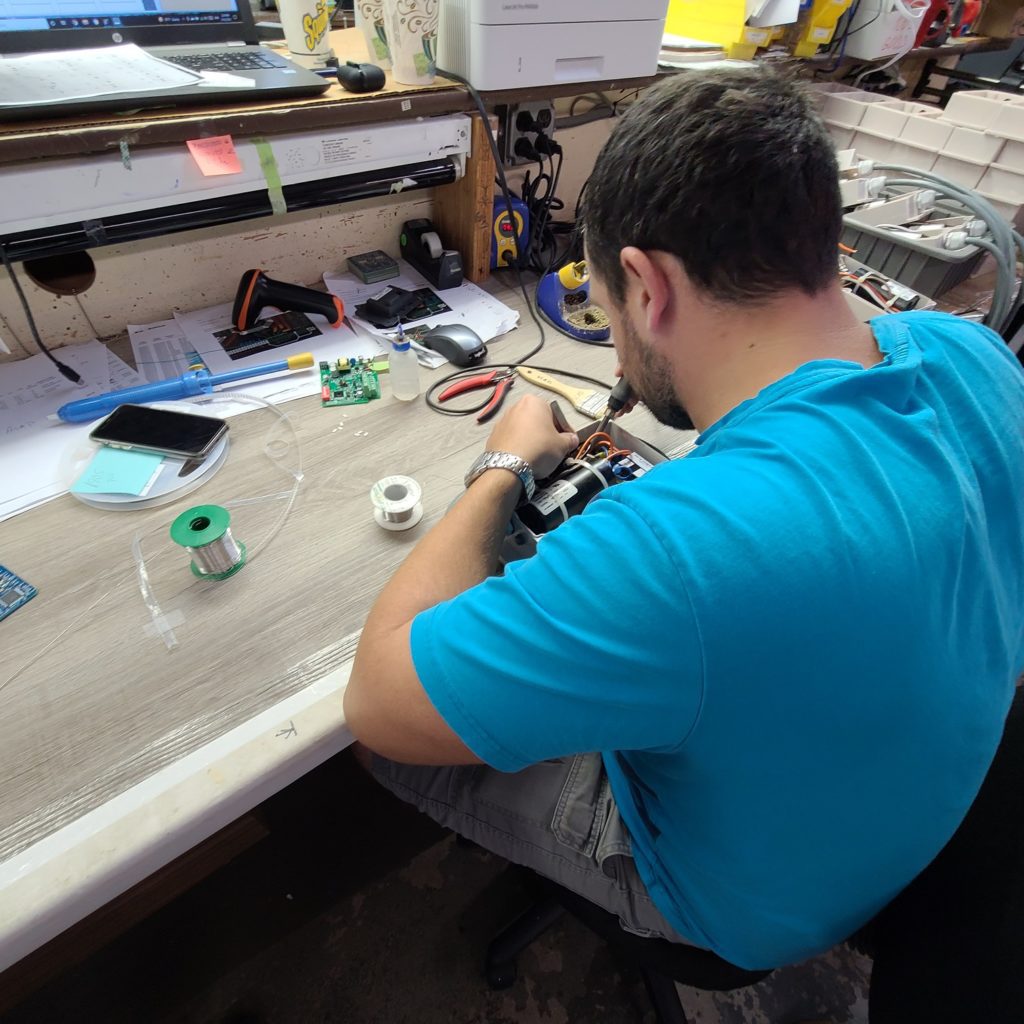
After the retooling station is a long section of space with 4 rows of work stations. One against each wall and two face to face down the center of the room, so that pieces on line can be completed, then handed to the next station on their way down to packaging.
When we were chatting with Kevin in the conference room about their products being built by hand, I had assumed he meant “built by hand”. You know, the same way everything is “built by hand”, a connection here or there was done by a human, but the most of the parts were put together by some super efficient robot.
Nope. Kevin meant Built By Hand. With Pride and attention to detail like the phrase American Made was meant to encompass.
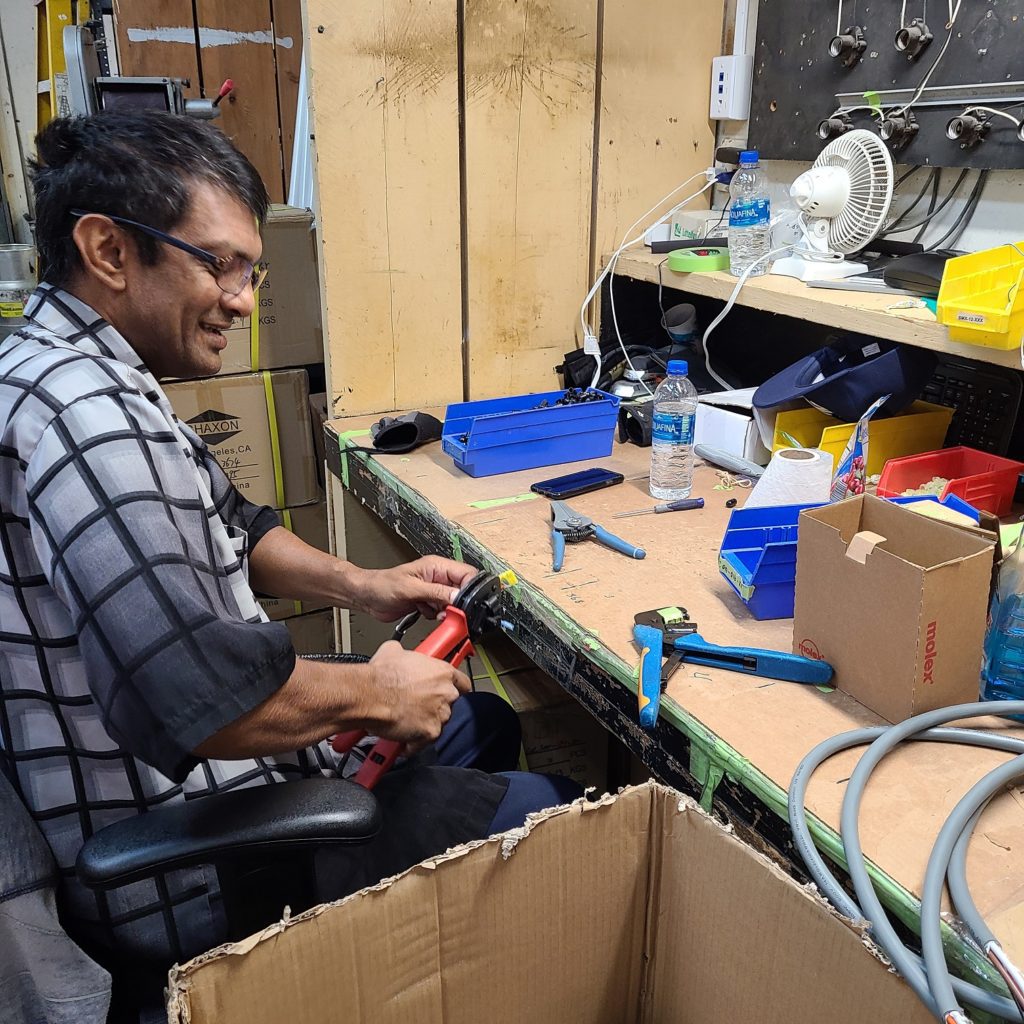
It was seriously impressive to see all the things that “used to” be made by American Craftsmanship actually being done by real humans who enjoy what they are doing. Hand crimped wire ends, Hand soldered wires, Hand tested controls, Hand done weatherproofing, Hand assembled circuit boards.
One thing you will notice in the pictures of the tour, is People. People doing everything. In fact, there is only one machine doing anything in the entire place. Its a relatively recent addition to the line too. Right next to it is its “hand made” predecessor that was only replaced because of the need to make more complex circuit boards with multiple layers of pathways.
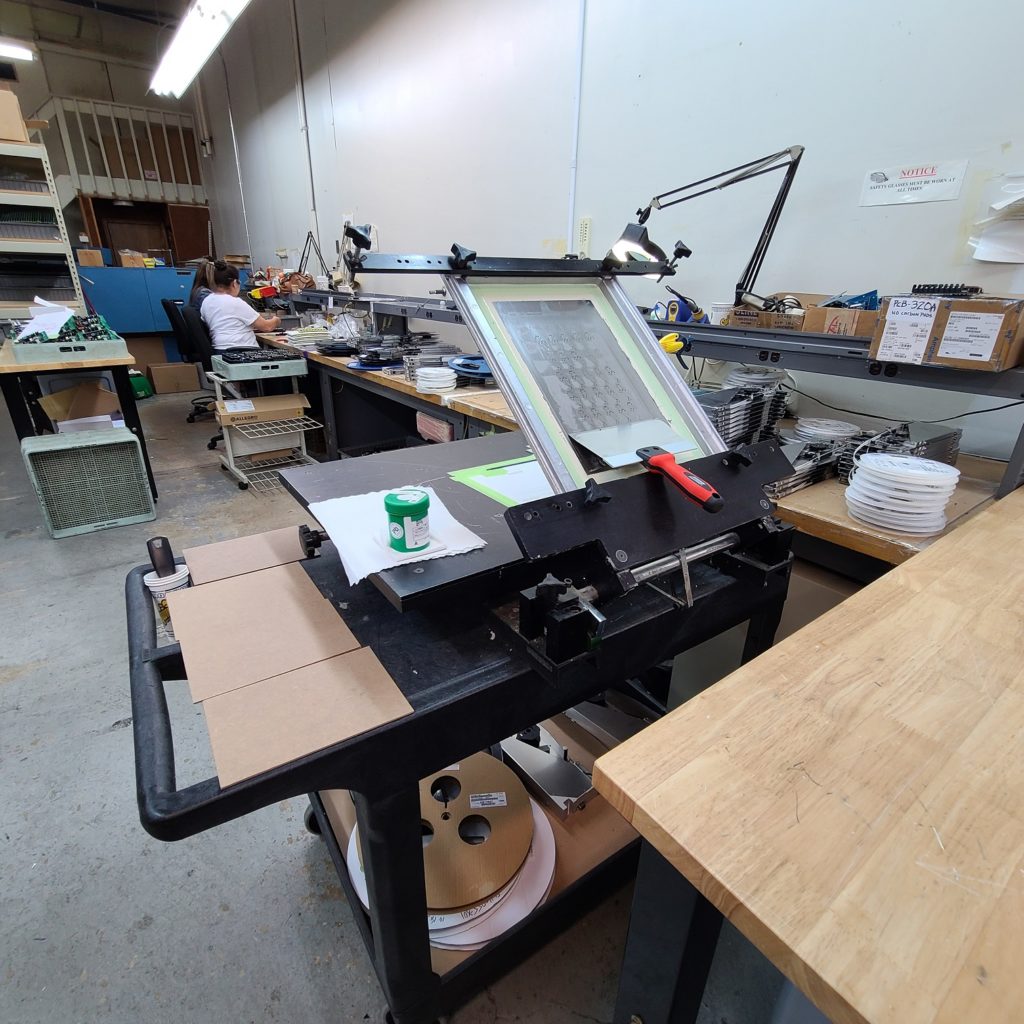
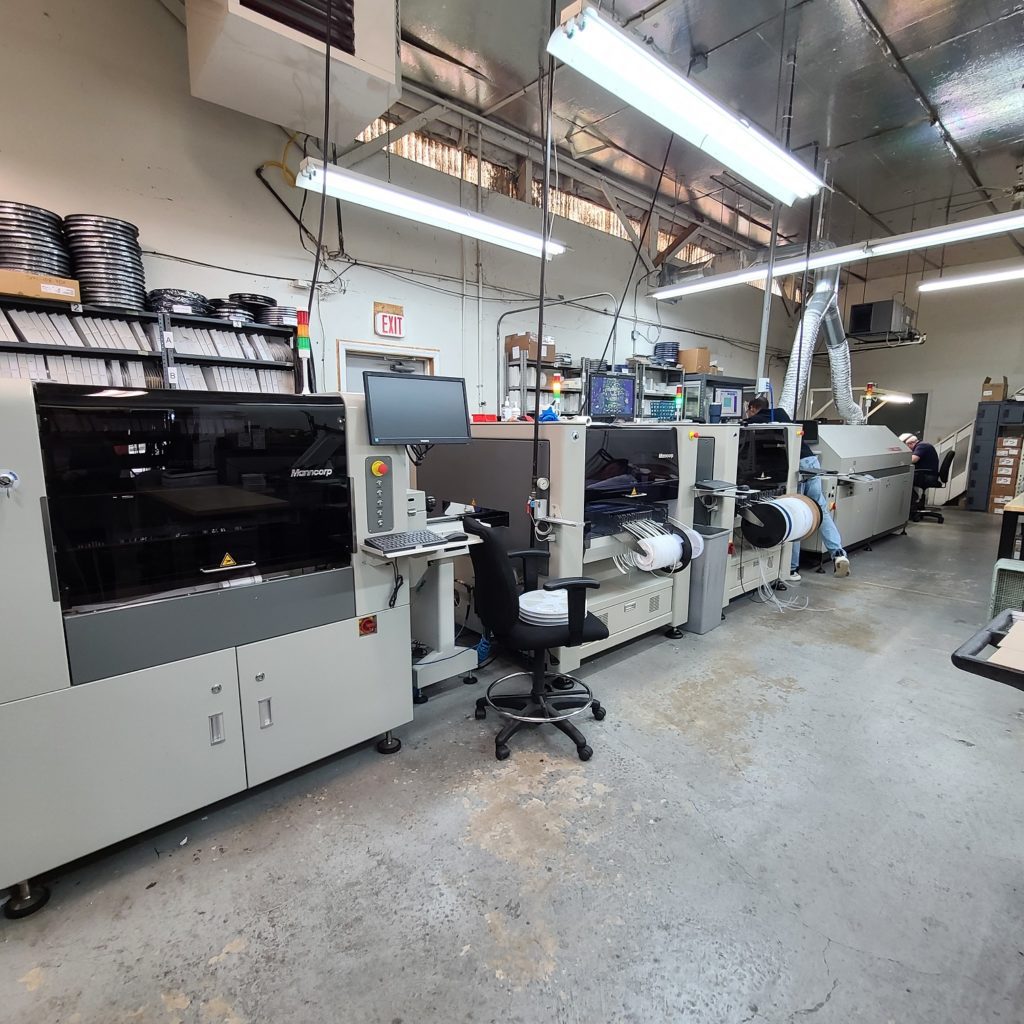
Now I know you may be thinking, “so much for hand made, this thing is doing most of the work”. Nope, not at all. Think of it like making dinner. You do all the prep, all the cooking, put it all together on the plate and serve it. This machine just makes the plate,
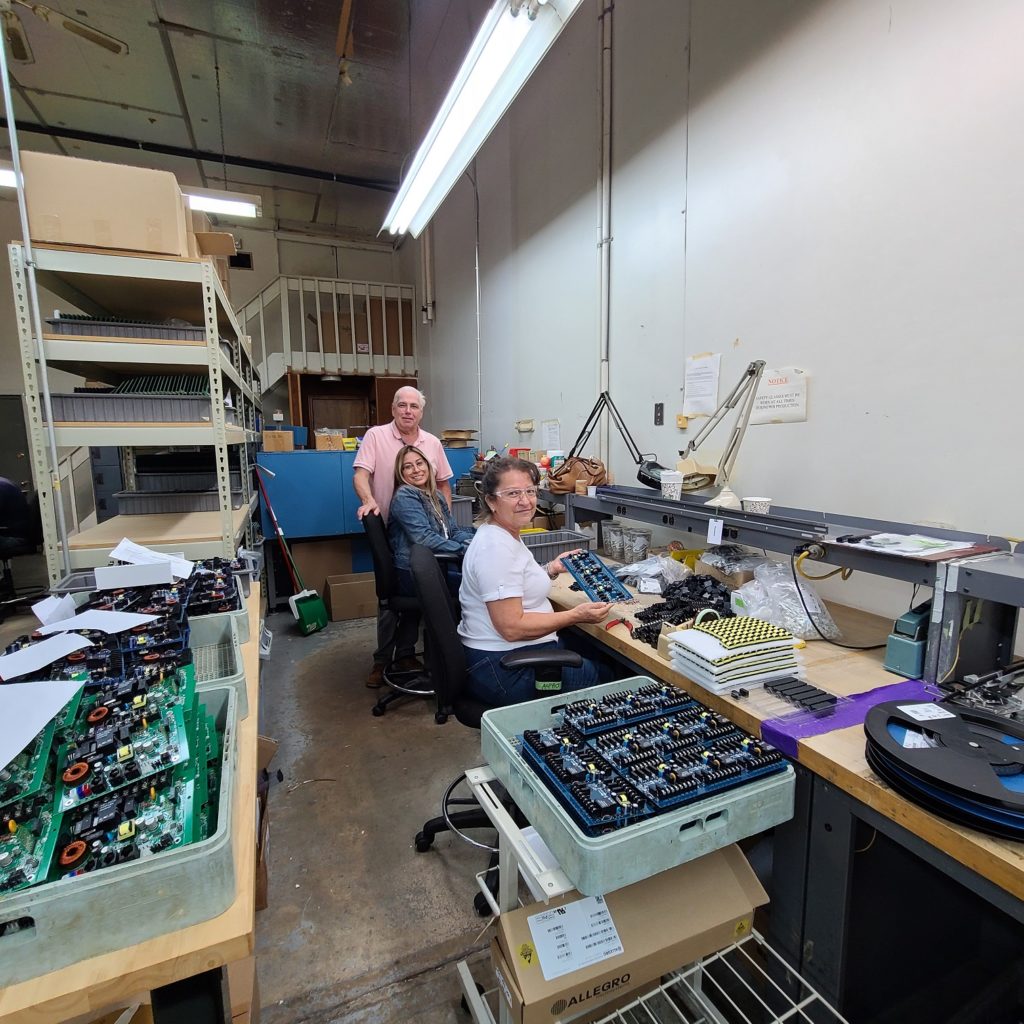
These two lovely women are the ones who put the small components on the circuit boards by hand so that they can be passed on to the proper assembly lines whether it be for RV or Marine use, Air conditioners or Thermostats, or any one of the various other products that Micro-Air makes.
If you recall the first thing I noticed when we walked in the building was chatting. That was a common occurrence throughout our tour. Now, in no way am I suggesting that everyone here should be diligently ignoring their coworkers and just mindlessly cranking out products for their consumers.
While taking this picture I had actually mentioned to Kevin that everyone here seems to be in a great mood and that this must be a great place to work or everyone here is really good actors. We all spent some time chatting and joking around about who was going to win the Academy Award for Happiest Employee, and in doing so came to learn that smiles like that can’t be faked.
Many of the people here have been here for their entire career. This is one of those places where you get hired as your first job and end up retiring from. The atmosphere throughout the factory is pretty laid back. Everyone enjoys what they are doing and actually likes coming to work and it shows in the products they put out.
I personally have Micro-Air products on my RV, and that was from before the factory tour, which made number 1 on my must have RV Upgrades list.