I recently got the opportunity to tour the Chris King Precision Components Factory headquarters in NW Portland. Although I’ve been living in Portland, Oregon for most of my life, I’d never visited the HQ and factory until a couple weeks ago when I was given a personal tour of the facility by Jay Sycip, Chris King’s head of marketing. Despite having zero experience working in manufacturing, and being an adequate but certainly not expert bike mechanic, the experience was nonetheless a fascinating and enjoyable one. And, having recently been testing the new Chris King ARD44 carbon all-road wheels, I was keen to see what goes into making these outstanding wheels firsthand.
The tour began with a history of Chris King components, highlighting the company’s breakthroughs and milestones on its path to becoming a legendary manufacturing company. The display cases filled with componentry served as not only a timeline of Chris King but in many ways of the bike industry as a whole, as King focuses on the parts that have seen the most change over the last 40 years of frame evolution in both road and MTB. Starting with a 1” threaded headset and moving through time to the new Aeroset and R45D hubs, it’s a spirited start to the tour that gives some high-level perspective on how influential and yet adaptive this company has been.

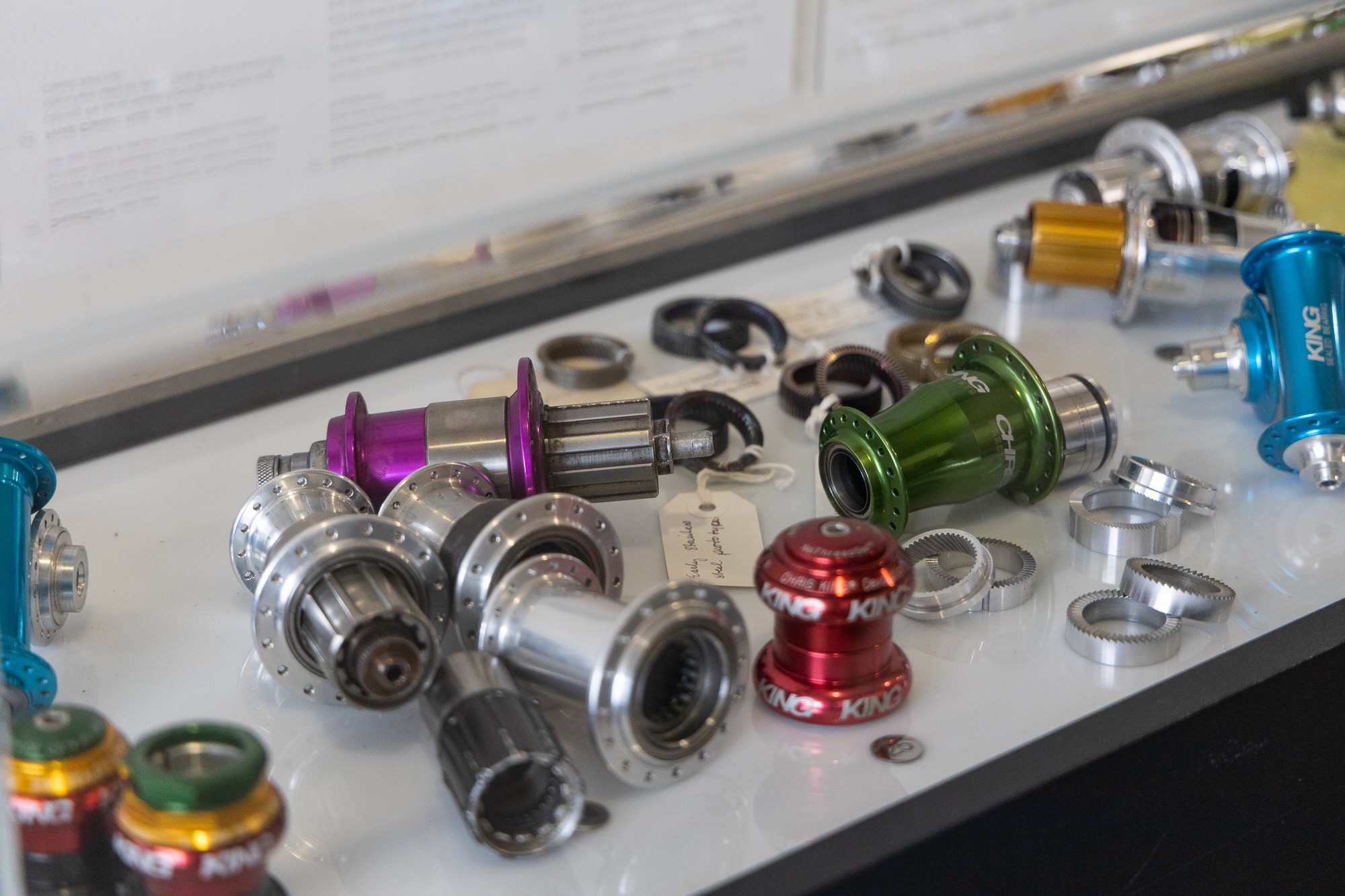
The King facility hasn’t always been home to ultra-refined wares, though. Sycip tells me that Folgers Coffee was once ground and distributed out of this building. Thankfully that smell has been replaced by aluminum and the vegetable oil that’s used to lubricate the machinery, and Stumptown Coffee is available in the cafe.
We start in an area that contains aluminum stock, which is in the form of long rods that will eventually shed a significant amount of material to become finished components. That excess material is consolidated into large pucks to make recycling viable. According to Sycip, if the material wasn’t compacted, its volume would fill much of the facility. King makes sure that each puck is recycled, which is an example of its well-documented record of being a sustainable company. Next to the aluminum stock is a fenced-off area dedicated to testing new tooling before it’s implemented on the shop floor. It’s run by a fellow whom Sycip tells me has been at the company for 30 years, and relocated to Portland with the company when it moved operations from its former home in Redding, CA.
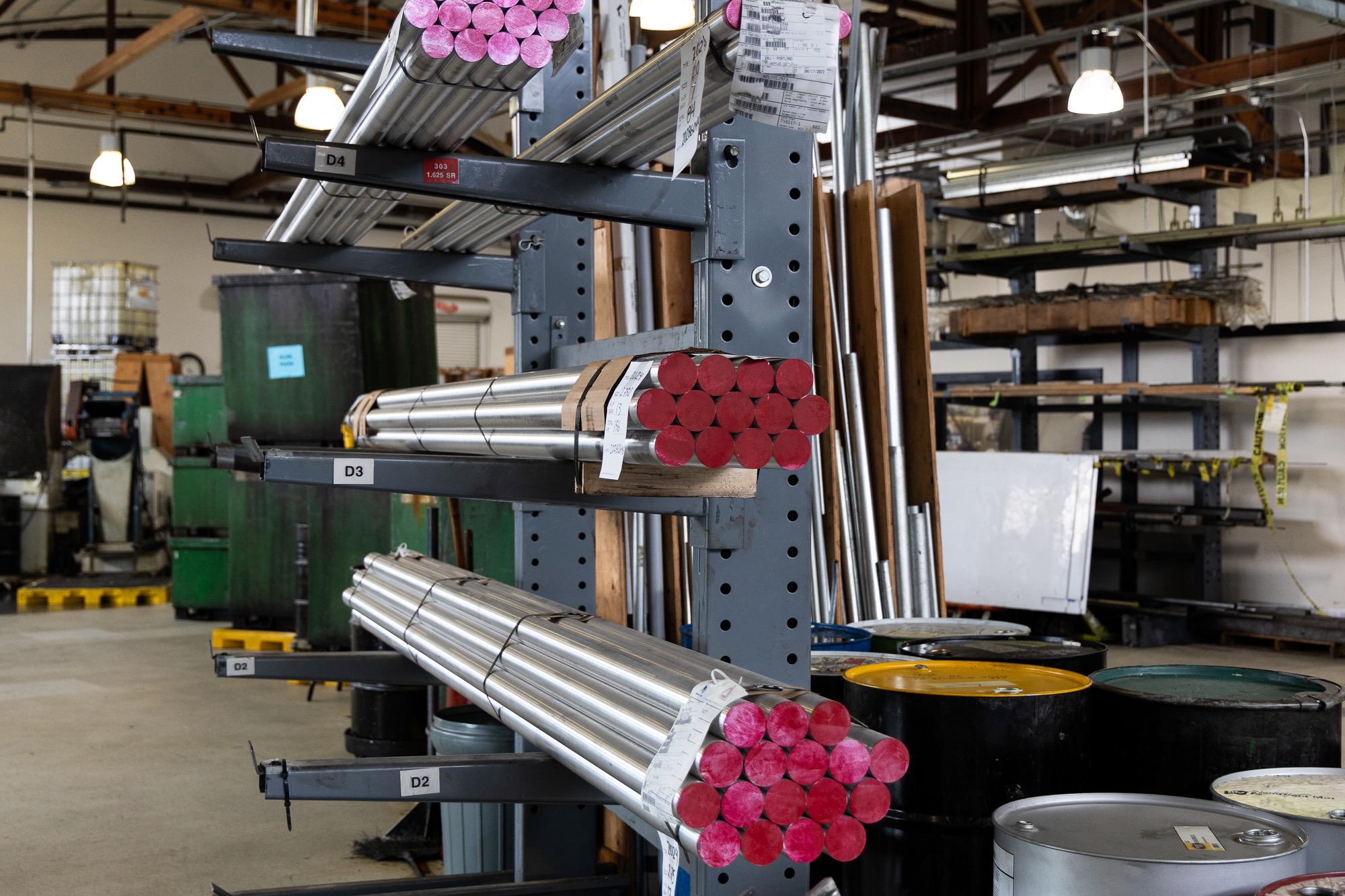

Like any factory, there’s an interplay between powerful machinery, and the human ability to analyze and organize. In the King factory though, there’s an almost warm and fuzzy feeling, as it’s easy to observe pieces of aluminum being transformed into functional art that will one day grace beautiful bicycles. I’m especially keen to see the manufacturing of hub internals, as I’ve been testing the ARD44 wheels that feature the R45D hubs.
Peering through windows splattered with vegetable oil, I watch as hub shells are bored out as thin as possible, center lock splines and freehub bodies are carved, and drive rings are sculpted. Eventually, I watch as a batch of hubs are cradled inside a chamber and laser etched with the Chris King logo. The entire process feels intimate and joyful, but at the same time, it’s clear that people are working hard, doing things perfectly or as close to perfect as is humanly possible.
Accuracy is the central theme of Chris King’s manufacturing process, meaning that the machining tolerances of all the pieces that fit together inside King hubs, headsets, and bottom brackets are extremely precise and that precision is constantly being verified by manual measurement at every phase of the process. In many cases, every 10th part to finish a given machining process is measured to ensure that the machine is operating within tolerance.
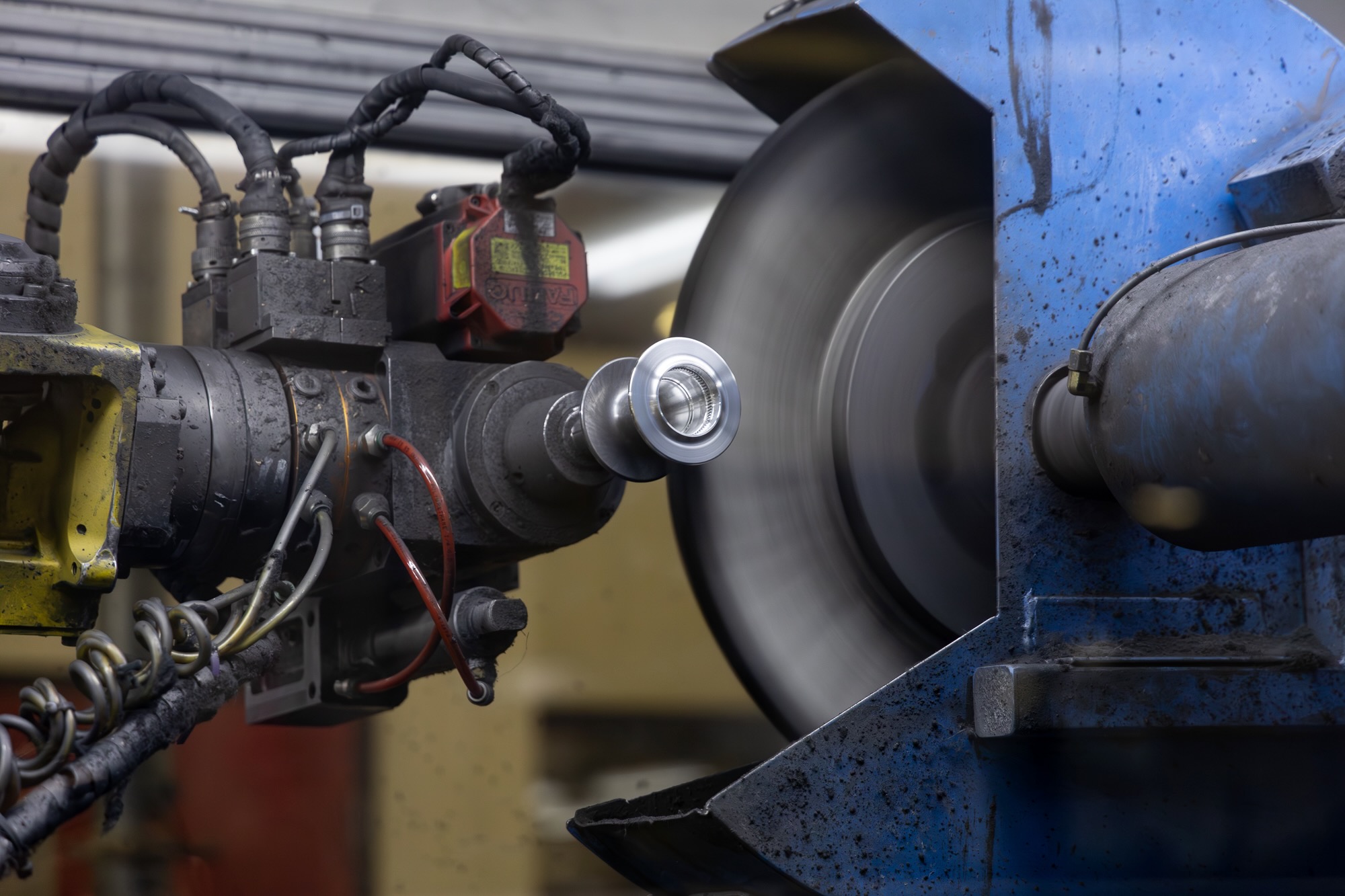

One of the more satisfying stops of the tour was to watch a massive robot pluck hub shells off of a tray before spinning around to hold them up to one of a series of high-speed polishing wheels, rotating the hub shells subtly to ensure every nook and cranny of the surface was evenly polished. In other parts of the facility, different stages of polishing are being done manually, or by submerging parts in giant tubs of walnut media that churn throughout the day.
Once a hub is drilled for spokes and anodized, it is what it is. So, King pauses production of hubs at various stages, based on what’s been sold and needs to be replenished. Seeing components – especially hub shells – at various stages of manufacturing was seductive. Before being anodized and drilled for spokes, the hub shells are quietly alluring, sitting in crates on shadowy shelving, gleaming proudly, waiting their turn. In this almost-finished state, it’s easy to see why so many custom and small batch frames end up with King hubs – their organic shape and timeless looks can surely tie a bike together visually.
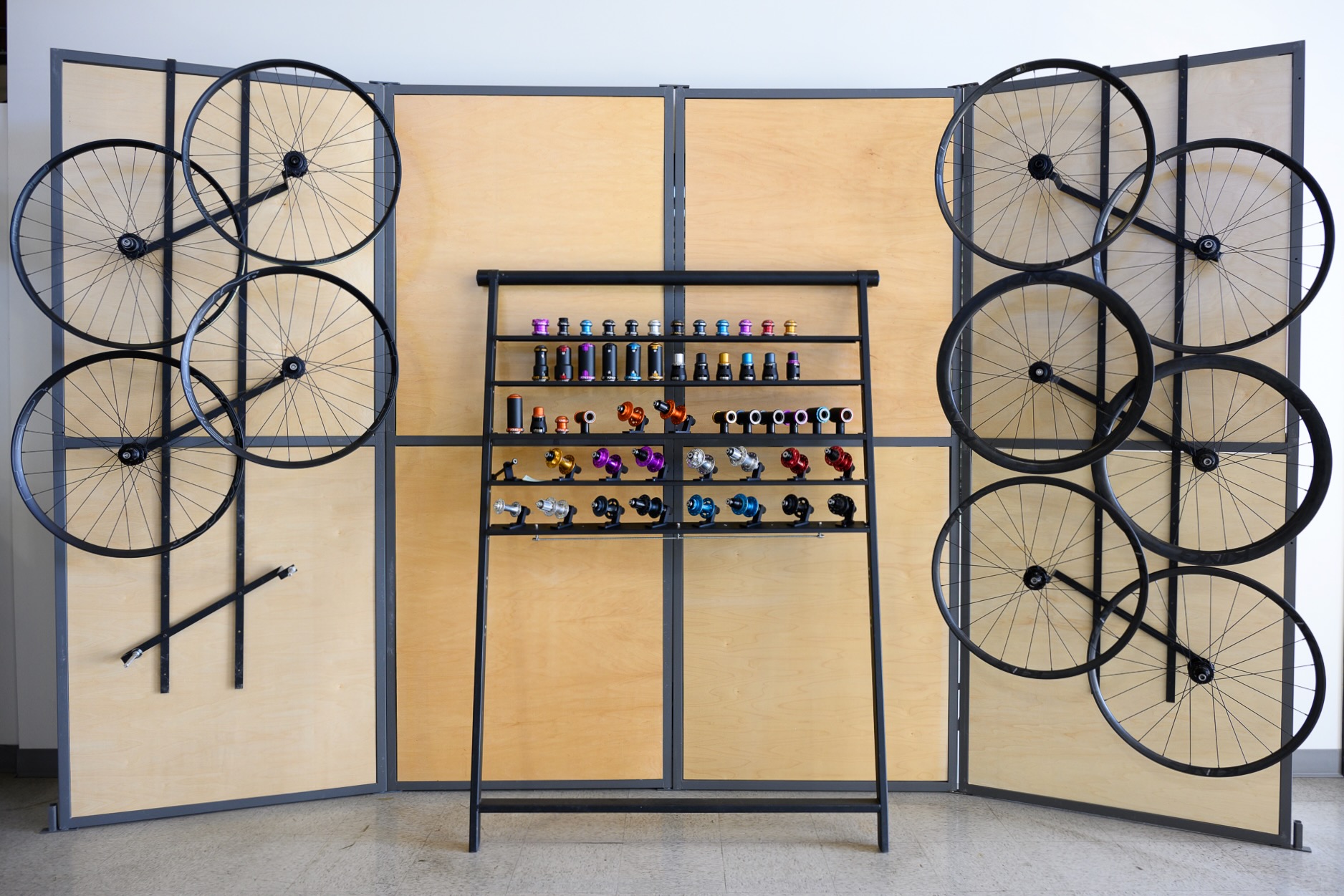
I came away from this tour with a new appreciation of the phrase “You get what you pay for”. What you’re paying for when buying a Chris King component is an uncompromising commitment to precision in manufacturing and employee care. The operation struck me as being efficient by way of patience and forethought, not by frantically paced output that burns people out. Even with the use of incredibly powerful machinery, this factory moves at a deliberate and methodical pace. The lean crew of workers is super focused, performing repetitive tasks as though it were a surgical procedure. Everyone seems happy to be there and is genuinely friendly and interested in discussing what they’re doing.
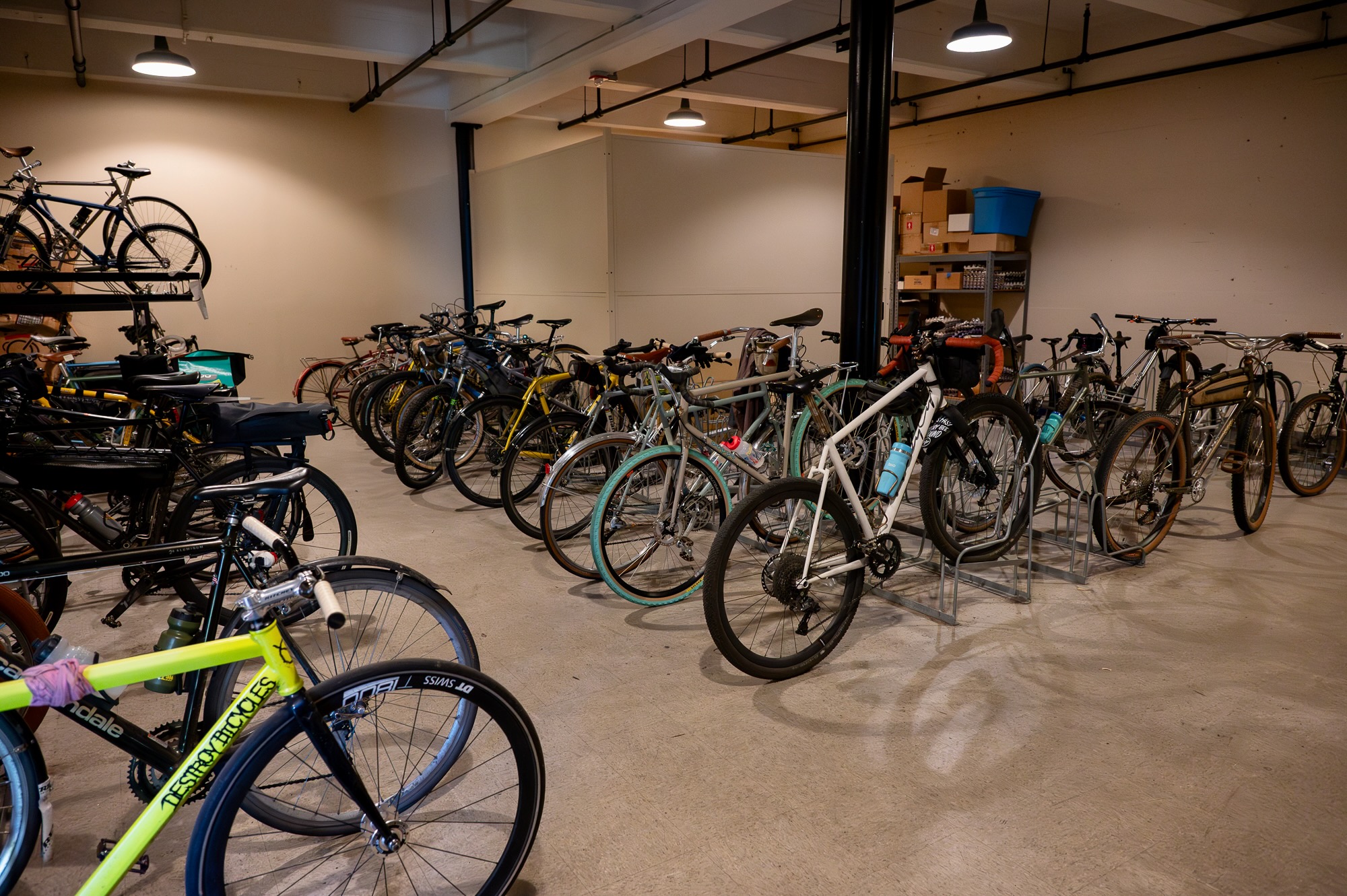
Employees are offered many perks, most of which focus on riding more. First, they simply get paid to commute to work. While this used to be provided in the form of meal credits, it’s now cash that’s added to their paycheck. The locker room has health club-level facilities including a nifty ventilation system that pulls air through the lockers to dry out clothing that gets damp on the morning commute. Full tune-ups and other mechanical assistance for employee bikes are available in the service and warranty department. Above the shop floor is a comfortable cafe area, and a main-level corridor is lined with ping-pong tables where things get pretty rowdy every day at around 3:00.
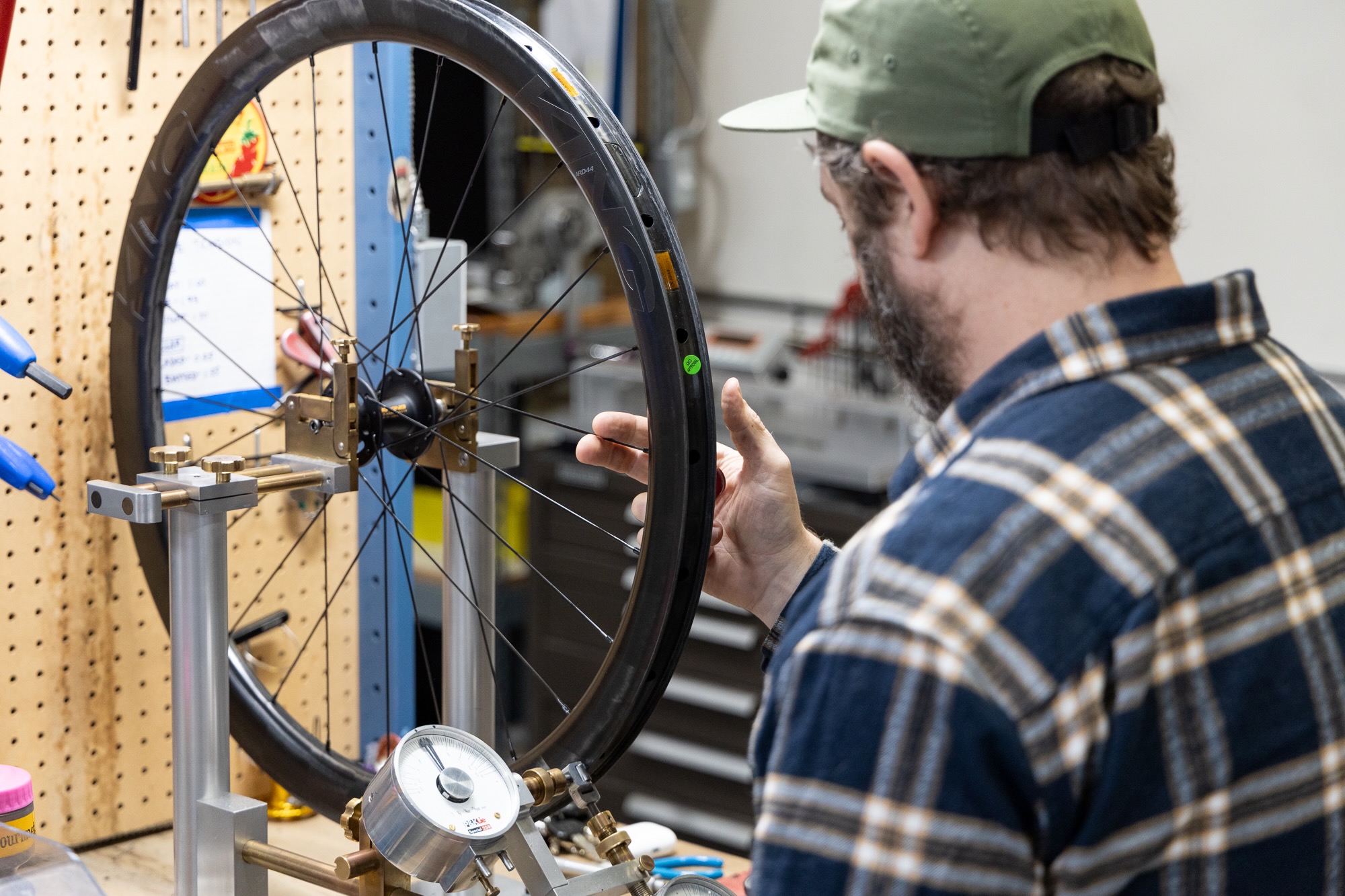
Visiting the wheel building area, I watch as a set of the new ARD44 wheels are in the final stages of production, being trued and dished. The rims, which are made of fibers that can be recycled, combine with the R45D hubs to create a stunning wheel that is both at the cutting edge of technology and looks purely timeless and classy on the truing stand. But how do they ride?
Chris King ARD44 Fusion Fiber Road Wheels Review

Chris King’s first foray into carbon fiber road wheels is in many ways exactly what I expected from the brand – a supremely refined, faultless, and beautiful wheelset that feels like it just might last forever. One of the biggest stories here is the innovation in the rim of the ARD44, which consists of a material made by a Utah-based firm called CCS Composites and known as Fusion Fiber. These carbon rims use a thermoplastic resin, instead of the thermoset resin that has until now been used to mold most carbon fiber rims. This thermoplastic resin process claims to enhance the fiber’s ability to absorb impact and vibration, and on the road, makes the ARD44 rim magnificently comfortable, maneuverable, and steady over the roughest surfaces.
Fusion Fiber was first applied to MTB and gravel-specific rims by companies like Forge+Bond and Revel, and the Chris King ARD44 is the first road wheelset to utilize this new tech. Not only are they super comfortable for their 44mm depth, but the thermoplastic resin makes the rims recyclable when the time comes, which by the feel of the ARD44 wheelset, will probably be long, long after you’ve moved onto a new bike.
Aside from buttery ride quality, the other arresting feature of the AR44D is its unwavering stability. In the context of deep-section carbon wheels, “stability” is typically associated with a rim’s ability to cope with hectoring crosswinds. Deep-section carbon wheels of yesteryear were notoriously sketchy in the wind because fast-moving air would detach from the rim surface rather abruptly, kicking off a ripple effect in the front end of the bike, causing the rider to feel like their front wheel was being pulled out from under them in an unpredictable way.
More recently, advances in the dimensions and profiles of carbon rims have dramatically improved crosswind stability industry-wide, but some rims still feel more stable than others in this situation. In varying wind conditions, King’s ARD44 rim is the most stable-feeling rim deeper than 30mm that I have ever tested. The ARD44 simply does not wobble or experience any lateral pulling or pushing as they cut a path through gusty conditions. Maneuvering stability is also top-notch, bringing new levels of confidence and control to technical descents on less-than-ideal pavement and gravel.
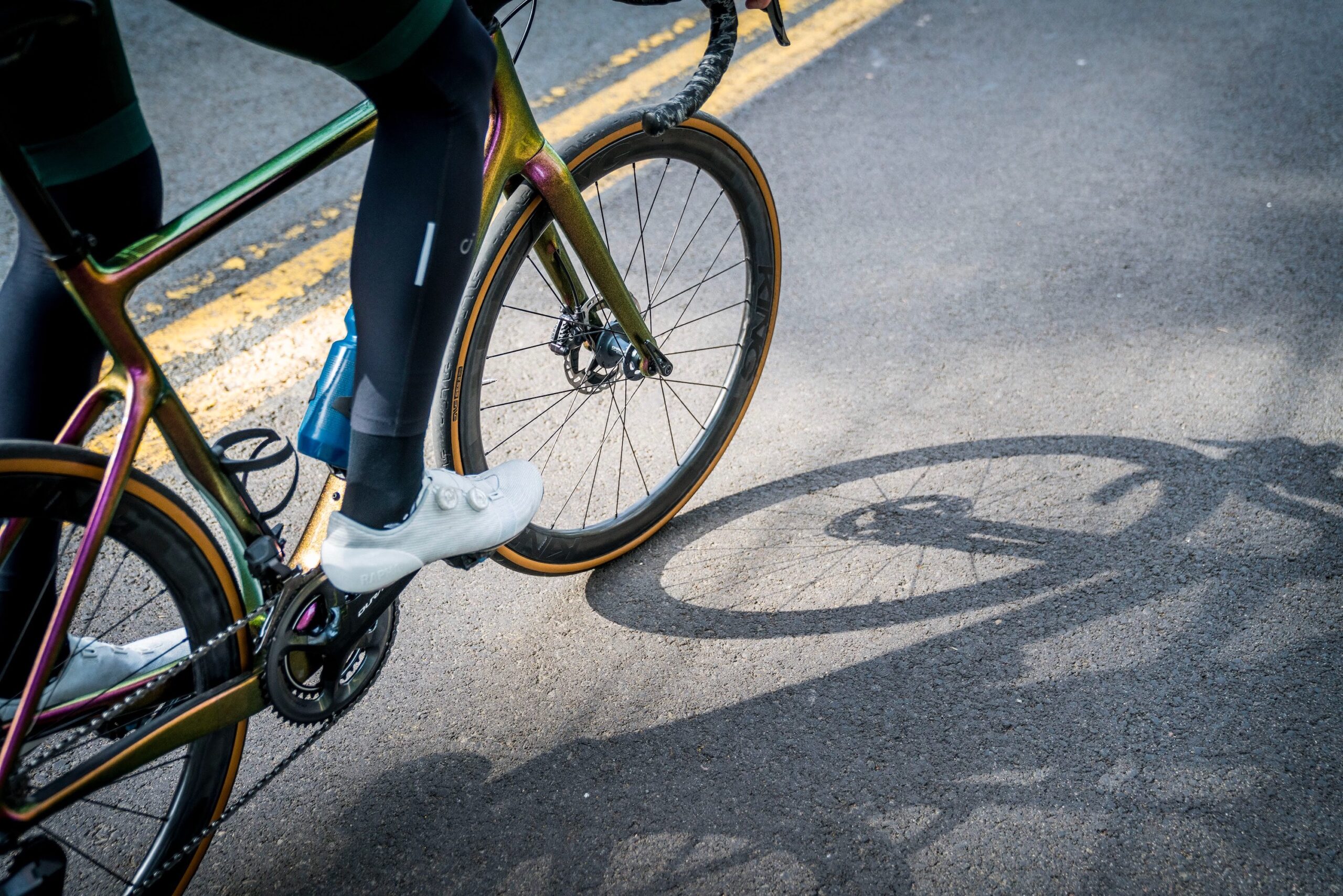
Additionally, the ARD44 is audibly more stealthy than many other carbon rims. While some racers love the walloping “whoosh-whoosh” of many deep-section rims, I quickly became a fan of how much more of the world around me I could hear when riding the ARD44. This can most likely be attributed to the impressive damping properties of Fusion Fiber which seems to mute noise as well as it does vibration.
The ARD44’s hookless bead wall, 25mm internal, and 30.5mm external width will likely appeal more to the all-road and gravel crowd who run slightly wider tires. King does state that the ARD44 are “aero optimized” for 28-30c tires and claims they can accommodate tires up to 47mm wide. That said, according to ETRTO guidance, road riders can safely run 29c tires with pressure in the 70 PSI range, without any safety issues, so I’m sticking with that. But, we’re sure that the folks at Chris King have done their research and testing, and for more info on tires and the ARD44, you can read Chris King’s tire compatibility statement here. And yes, there are some tires out there labeled 29c, such as the ENVE SES, to name a favorite of mine.
Furthermore, the ever-increasing choice of supple and hookless-compatible road tires means that one of the major knocks against hookless – their incompatibility with clincher tires – is becoming less of an issue. Regardless of public opinion on hookless rims for road riding, some of the biggest names in the industry, like ENVE, Zipp, Giant/Cadex, and now, even Chris King, are on board with hookless road. Bottom line, if you’re not comfortable riding hookless rims on the road, that’s fair, there are lots of other options. But given the reality of thousands of hookless rims being safely used on the road within the guidelines of ETRTO, we’ll keep seeing them on many of the best road wheelsets on the market, the ARD44 included.
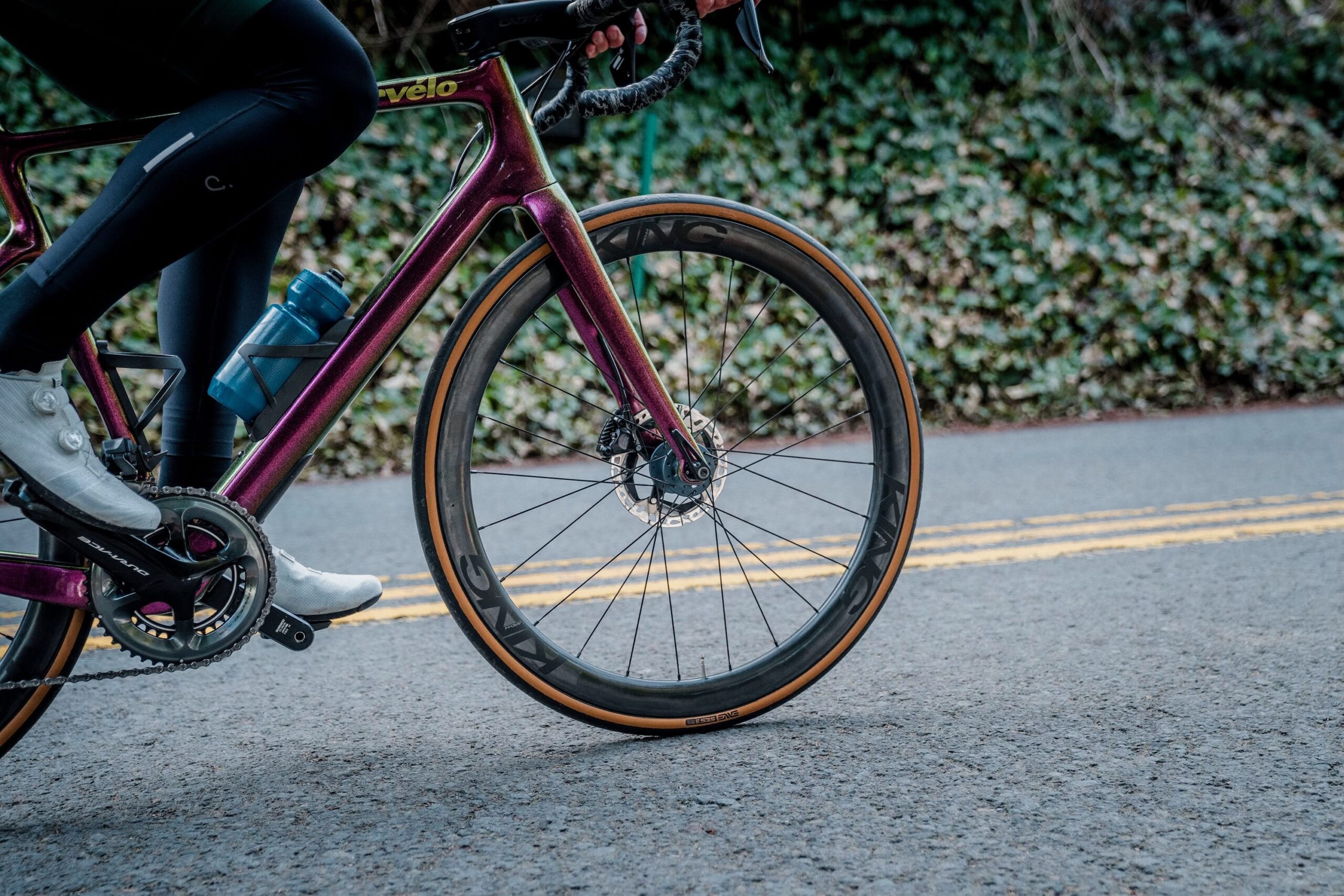
Moving to the rest of the ARD44 build, we find one of Chris King’s best components, the R45D hub, which offers another kind of stability that can be felt through the bike’s drivetrain. With 45 points of simultaneous engagement, the Ringdrive system in the R45D hub brings a gloriously quick, smooth, and yes, stable feeling to hopping out of the saddle and hitting the gas hard. After watching all the individual pieces being machined in the factory, it was not surprising that the ARD44 wheels feel perfectly anchored and balanced by the R45D hubs. I was even impressed with R45D hub’s engagement after riding the DT Swiss 240 Star Ratchet system for a long time. While the DT Swiss system is also excellent, there is a markedly more instantaneous and smooth response from the R45D rear hub during big accelerations.
On the topic of hubs, the ARD44 wheels can be ordered with your choice of Shimano HG, Shimano Microspline, and SRAM XDR freehub bodies. They come with smooth-rolling stainless steel bearings, and buyers have the option to upgrade to ceramic bearings for a $110 increase in price. In typical Chris King fashion, you can also choose between 10 different anodized color options if you’re trying to color coordinate on your dream build.
The hubs and rims are laced together with quality Sapim CX-Ray bladed J-bend spokes. These spokes help to reduce aero drag and enhance that comfortable ride quality. Plus, they should be reasonably easy to find if you ever need to replace one. The ARD44 rims weigh 435 grams, and the complete wheelset comes in at 1525 grams. While these are certainly not competing for best-in-class weight figures for a wheelset at this price point, it’s important to remember that the ARD44 isn’t designed around a myopic focus on weight. These are wheels that are intended to provide comfort. stability, and are built to last a lifetime.
To that end, King offers an excellent lifetime warranty that is simple to understand and use. Assuming you are the original owner, if you inflict harm on your ARD44 rims, you can send them back to Chris King for a new rim and rebuild using the existing hub – which will also receive an overhaul at the same time – they even pick up the cost of shipping both ways. What this warranty means in practice is that these rims are bombproof. Chris King doesn’t want a pile of cracked rims getting replaced for free, so they only offer this level of support because they trust the failure rate will be extremely low.
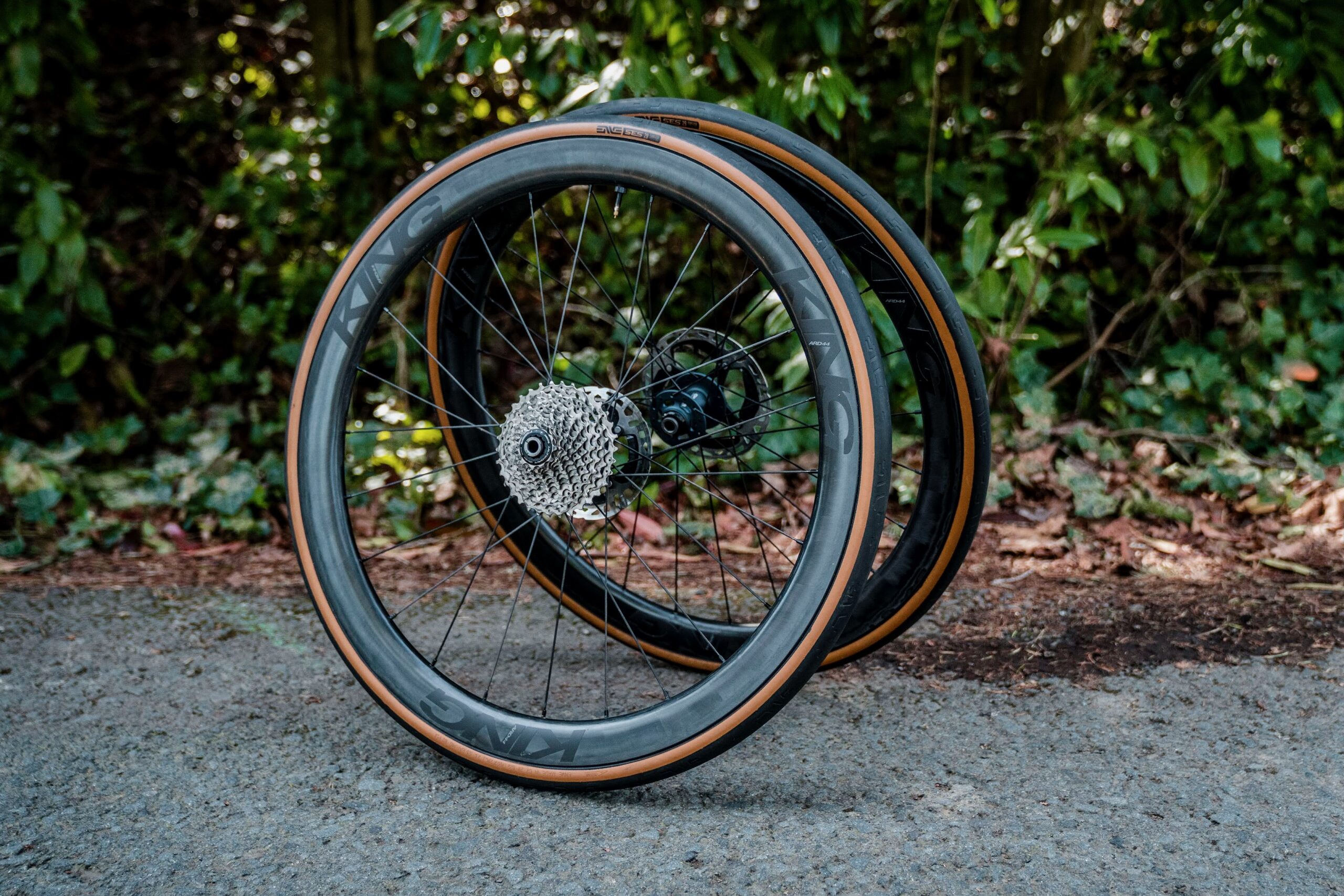
At $2850, these are undoubtedly a high-end wheelset, but the price of the ARD44 is aligned with other premium road wheel options. And, though they may not be the lightest, they are impressively comfortable, stable, and elegant-looking all-around road wheels made to the highest standards and meant to last a lifetime on your forever bike.